Bearing Condition Monitoring - Bearing Acoustic Lubrication
Bearing Condition Monitoring – Acoustic Bearing Lubrication
The most important part in bearing maintenance is LUBRICATION. Contaminated lubrication, Over Lubrication, Insufficient Lubrication and Hardened Grease are the major reasons of most of the bearing failures.
Hence, scientifically managed lubrication (Acoustic Lubrication) is part of our Bearing Condition Monitoring program.
The most important part in bearing maintenance is LUBRICATION. Contaminated lubrication, Over Lubrication, Insufficient Lubrication and Hardened Grease are the major reasons of most of the bearing failures.
Hence, scientifically managed lubrication (Acoustic Lubrication) is part of our Bearing Condition Monitoring program.
OUR PRODUCT:
1.Condition Monitoring of the Bearings with (Triple NDT methods) Vibration Analysis, Ultrasound Analysis and Thermography including Ultrasound Guided Greasing of Bearings (Acaustic Greasing)
2. Condition Monitoring of Bearings, with Vibration Analysis, Ultrasound Analysis and Thermography (No Greasing Program)
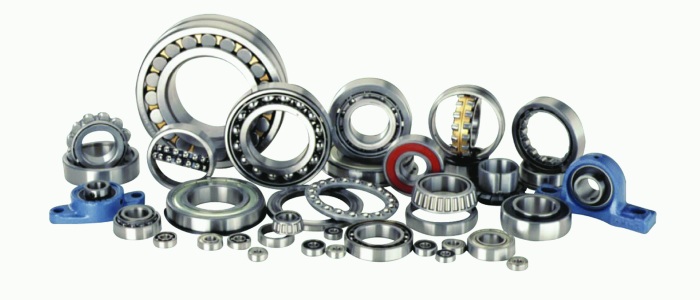
Bearing Condition Monitoring
Most important point to be noted here is, condition monitoring measurements of any equipment has to be done with same measuring instrument at same location by the same method every time of measurement during the period of CM.
Most important point to be noted here is, condition monitoring measurements of any equipment has to be done with same measuring instrument at same location by the same method every time of measurement during the period of CM.
A. Under this, we generate ‘BASE DATA’ of all the given bearings through Vibration Analysis, Thermal Mapping, and Ultrasound Analysis.
a) Base Data through Vibration Analysis – We not only carry Vibration Measurements but we do Vibration Analysis on given bearing and the base data includes,
- Vibration FFT analysis – the data is captured setting the range of measurement looking at Fundamental Frequency (bearing rpm – 1 x) and its harmonics (2x, 3x, 4x etc). The Waveforms and analysis report is maintained as base data.
- Vibration Time Analysis (Optional) – The time waveform is captured along with FFT, analyzed and kept in record as base data.
- Vibration Measurement Readings taken at Vertical, Horizontal, and Axial direction of the bearing under CM.
Here the points of measurement on bearing are marked permanently and the instrument used is noted down. And the measurement is taken on same marked points with same instrument during next all measurements of condition monitoring.
b) Base Data through Ultrasound Analysis – The Points are marked on bearing housing (permanent) and the ultrasound readings are taken at that point. The Peak, RMS values of ultrasound and the crest factor is recorded. The graph is saved. This data will then be compared with further measurements taken under CM program.
c) Base Data through Thermography –The bearing is mapped thermally from specific defined distance and angle. The distance and angle is noted down in the data. The thermogram is saved to compare with further thermograms those will be taken during CM program.
Important: We might locate few bearing faulty or under-lubricated or over lubricated during this survey of base data. In that case, we request/ suggest customer to replace the bearing or re-greased it. The data is taken again after corrective action. And the data taken after corrective action will be recorded as ‘Base Data’ of that bearing.
![]() |
![]() |
B. Condition Monitoring Visits, Trend Analysis
- After Base Data generation, depend on conditions of bearings, the frequency of condition monitoring visits for particular bearing will be scheduled. (This means for the bearings under higher risk, higher frequency of visits will be scheduled, say weekly/fortnightly and for bearings having lower risk, lesser CM visits will be scheduled.) This schedule can be changed time by time for particular bearing, after correction or after developing fault in it.
- Visits for condition monitoring will be made as per scheduled program.
- When ever found any anomalies in any bearing during monitoring, will be immediately informed to customer and mentioned in record/ report with suggestion of corrective action.
- After every CM visit, the readings, / measurements of VA, UA & IR are taken in trend analysis. The report of trend analysis will be given after 3rd CM visit onwards, with CM visit report.
Ultrasound Guided Acoustic Bearing Lubrication (Greasing)
![]() |
![]() |
Under this program bearings will be greased only when it is necessary and with the exact quantity of grease (No under-Greasing – No over-Greasing). Hence, the quantity of grease can be saved which is not possible in preventive maintenance program. In preventive maintenance, bearings are greased on scheduled intervals, without knowing whether it requires greasing or not. Hence, always the quantity of grease required increases and problem of over-greasing may introduce.
Wherever required the contaminated grease will be removed off and fresh grease will be filled to the necessary quantity with the help of ultrasound equipment.
Procedure: The ultrasound Equipment is kept measuring the Ultrasound that generated from bearing while greasing the bearing. There will be higher noise from bearing before started greasing and at one point the noise reduces drastically. (Refer the graph herewith). The greasing will be stopped at that point. If we keep greasing further, than again the noise will start increasing and that will be over-greasing condition.
Preface:
Bearing failure doesn’t only cost replacement of bearing but bearing failures might turn into catastrophic failure of complete equipment. Bearing never fails alone but it fails along with shaft, bearing housing (Cartridge), Machine Envelop.
Bearing failure immediately causes downtime, production failure, and immediate shutdown of whole machinery. This intern causes heavy losses to company. A small bearing can cause heavy losses……!
Also No Bearing runs till its whole designed life. Hence, the cost of bearings over a period goes 1.5% higher for a company, may go double.
And that is why bearing condition monitoring is important in company maintenance. We can maintain bearings such a way that, there will be NO BEARING FAILURE and bearing life will increase.
Wherever required the contaminated grease will be removed off and fresh grease will be filled to the necessary quantity with the help of ultrasound equipment.
Procedure: The ultrasound Equipment is kept measuring the Ultrasound that generated from bearing while greasing the bearing. There will be higher noise from bearing before started greasing and at one point the noise reduces drastically. (Refer the graph herewith). The greasing will be stopped at that point. If we keep greasing further, than again the noise will start increasing and that will be over-greasing condition.
Preface:
Bearing failure doesn’t only cost replacement of bearing but bearing failures might turn into catastrophic failure of complete equipment. Bearing never fails alone but it fails along with shaft, bearing housing (Cartridge), Machine Envelop.
Bearing failure immediately causes downtime, production failure, and immediate shutdown of whole machinery. This intern causes heavy losses to company. A small bearing can cause heavy losses……!
Also No Bearing runs till its whole designed life. Hence, the cost of bearings over a period goes 1.5% higher for a company, may go double.
And that is why bearing condition monitoring is important in company maintenance. We can maintain bearings such a way that, there will be NO BEARING FAILURE and bearing life will increase.